全球 2022-05-20
轉型、升級—老手與科技的融合,產線與數據的串聯
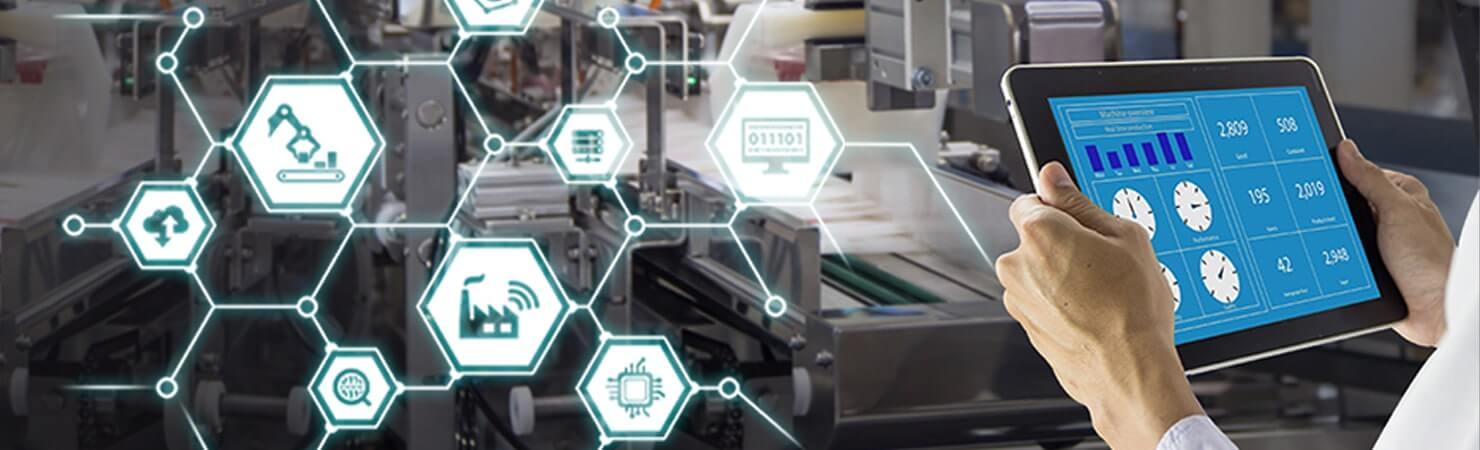
過去40年SIGMA在醫療滅菌產業已經累積了豐富的經驗,然而面對全球劇烈競爭的商業環境,數位轉型與經驗的傳承是我們要持續思考的重要議題。在歐美國家的創新科技、全球人力成本增加以及政經情勢變動的衝擊之下,「智慧製造」成為近幾年的熱門詞也被視為傳統製造業的轉型目標。自2018年加入明基材料,在集團持續推廣ESG理念之下,永續經營也融入SIGMA的企業使命,因此讓我們看見了產業轉型的契機,而過去兩年受COVID-19疫情影響日益增長的醫療包裝需求,也讓我們意識到運用科技為產業提供更可靠且更有效率的解決方案才能應對市場的挑戰。
結合明基材料在電子製造業的經驗以及完整的物聯網解決方案,SIGMA也於2021年開始布局智慧製造,本文將會分享SIGMA智慧工廠的建置,包含IE 流程及程序整合、AED自動化、AOI視覺開發...等,以及智慧製造的未來規劃。
用數據承接經驗
智慧化是未來的趨勢,疫情延燒下也持續推升數位轉型需求,隨著這幾年來科技快速發展,大數據分析、IoT物聯網、AI人工智慧,時常讓人看得眼花繚亂,然而這些數位化的目的是什麼?
智慧製造的基礎在於「數據」。不管是任何產業,都會以過去經驗來解決問題或做出決策,但這樣很難被系統化,經驗決策也缺乏客觀證據的參考,若能將工作流程中各項經驗轉化為數據,轉化成有建議性的分析結果或是方案,就能針對不足的部分進行改善。
舉例來說,偏光板不論是正翹反翹,都會造成客戶後續在貼合時造成無法吸附或是貼合後產生氣泡的問題。過往經驗會列出高達80幾項的可能因子,再來進行分析異常原因,因為變因過多,造成分析難度增加,資料整理也相當耗時,人工彙整也可能造成疏漏,造成異常難以快速收斂,也會進而影響後續產出時間。明基材料從去年開始導入AI執行偏光片翹曲改善,藉由IoT自動化數據整合分析歷史數據,將可能的關鍵因子由80個收斂至5個,並統計出最佳參數生產範圍,透過「人難以觀察」的數據關聯性,協助分析判斷,解決問題。
從自動化到智慧化
談到智慧製造,大部人可能會直接聯想到技術、機台設備自動化,然而自動化不等於智慧化,自動化只是智慧化的第一步,從自動化到智慧化還有一段路要走,包含各設備間的物聯網數據整合,遠端監控再到串聯AI技術形成預測模型,最後達成智慧決策。
2021年開始SIGMA雲林廠區也導入產線自動化,在製袋的部分導入自動化包裝,透過自動連續包裝取代人工套裝及成品輸送路徑最佳化的節能設計,不僅集中疊棧作業,也能節省87%的電力。針對製程中的監控,導入分條接頭檢測,並串聯機台參數到Fab monitor系統,讓我們可以有效的掌握製程變異。2022年初,ASRS自動倉儲系統也完成建置,不僅能充分利用儲存空間,系統化管理也能簡化進貨及儲存作業的時間,進行精確的庫存管理及資料處理。IT系統方面也將透過MES、WMS系統強化製品管理,對於生產追溯、庫存管理有更精準的掌握,未來也會導入模具/柔版管理系統,針對關鍵機台與工具進行壽命管控,來達到即時檢修以及前端異常預防的目的,來進行全面的品質管控。
AOI的應用則分為「光學檢測」及「視覺整合」,在三大製程中使用光學檢測,進行良率掌控。 AOI能針對捲料進行即時瑕疵檢測,印刷顏色的部分,則以量化的數據取得樣品顏色數值取代人為主觀判定,建立工廠與客戶端的量化標準;吹膜的部分則可以進行良率預估,避免大規模異常捲料產出;製袋放面AOI的裁切監控,能提高裁切的精準度,有效管控封邊寬度穩定性。AOI視覺整合方面,我們自行開發了手機APP,取代人工手抄點檢,針對各站報表直接進行掃描讀取,直接將資料傳輸到系統中,供人員直接做統整分析。因應集團推導的ESG治理,我們也同時實現無紙化,減少對於環境的影響,流程精簡化也可以對人力進行更有效的安排。
創造雙贏,大於產品價值的服務價值
投入智慧製造對於SIGMA來說不僅能降低成本提升產能,針對人力進行更有效的配置之外,也能強化與夥伴之間的關係。客戶最在意的品質以及交期能藉由量化的指標,進行更有效的掌控,對於醫療產業相當重視強調產品追溯性,我們也可以明確的提供監控數據。而智慧製造中一個很重要的階段就是結合AI將數據轉化資訊,變為可利用的資訊進而創造價值,SIGMA希望透過大數據、IoT串聯,整合各項系統,結合領域知識做出預測模型,並達到掌握彈性決策的核心能力。最終更希望與客戶形成更緊密的串連,來提高預測的準確性,希望可以協助客戶對於產品應用的了解。對於供應商,則能藉由銷售及庫存數據的監控及分析,提供更精準且彈性有效的採購及操作,建立雙方共贏的綜效。